Supplier Compliance
A better way to ensure raw material compliance throughout the food & beverage supply chain, starting with certificates of analyses, and ending with supplier scorecards. See It for YourselfDon’t let material variability jeopardize quality or compliance
Staying on top of your growing list of suppliers and shipments—lot by lot—is all but impossible using static lists and spreadsheets. In order to maintain today’s high standards, you need to get more granular. We’re talking ready access and automation down to each certificate of analysis (COA), truck inspection checklist, nonconformance, and more.
Sound daunting? Without digitization, it is. But Networked Supplier Compliance offers early warnings, real-time record keeping, and unmatched visibility to support smarter, faster, safer decision making.

Today, there’s a limit to manual operations
Even the best teams in F&B can only do so much. Manually analyzing every COA, verifying the specifications, inspecting each shipment, lab testing the lot quality, and documenting the entire process is beyond time consuming. It’s a recipe for high risk and burnout. And we haven’t even talked about corrective and preventative actions (CAPA) or supplier scorecards yet.
But there’s so much risk involved with skipping any of these steps. Or making a mistake when it comes to material compliance.
It’s time to change your approach. You’ve heard the phrase ‘work smarter, not harder.’ Smart supplier compliance is safer, too.
A more efficient, more compliant tomorrow
It is possible to know when there’s a material issue before it becomes a problem. Advanced AI and automation can make a real-world difference when you’re using the right tools.
TraceGains automates the comparison of COAs and specs, flagging potential nonconformances and letting you focus on the bigger supply chain picture. Reject out-of-spec shipments before they ever reach the dock, saving time and reducing risk. Supplier Compliance also aggregates and analyzes historical data helping you spot patterns and invest in strong suppliers.
Streamline risk management with digitization and build a better supply chain that’s basically future-proof.
React before things go wrong and invest in the right supply chain partners with these capabilities (and more)
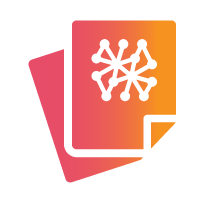
Automatically scan incoming COAs
With AI-driven tech, you can do more with COAs. Like read, compare, and qualify these essential docs, triggering out-of-spec warnings and other actions before the lot makes it onsite. Lowering risk and increasing accuracy all without reformatting or manually reviewing.
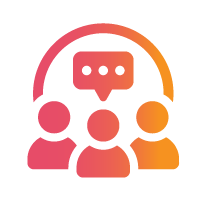
Communicate seamlessly across teams
Instead of sending the same emails, or making the same calls over and over, set up workflows that can alert your team about what’s going on. Without the need to log in or check for updates. Eliminate the back-and-forth between suppliers, shipping, receiving, QA, and more.
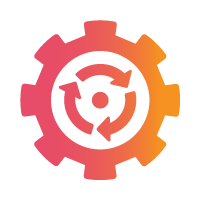
Manage & track CARs/SCARs
Track and manage any kind of nonconformance, linking associated audits, COAs and supplier data for easy reporting. When corrective actions are necessary, track them to resolution and tie them to preventative action plans and cost recovery.
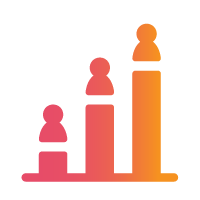
Compare supplier scorecards
Take those corrective actions a step further with configurable dashboards that let you scorecard suppliers and view trends. Ranking the best (and worst) parts of your supply chain on a regular basis.
AI-powered COA management
Unlock seamless COA processing with AI-powered automation, no more complex manual setup or field-level zoning required. Our intelligent document processing (IDP) solution extracts, validates, and categorizes COA data instantly, even from unfamiliar, non-standard or multi-lot COAs. Accuracy is high and improves continuously through adaptive machine learning. Say goodbye to inefficiencies and compliance headaches. Gain control over your material compliance workflow with real-time insights, fewer errors, and a smarter way to manage supplier data.
“Digitizing COAs and making them actionable through TraceGains has resulted in a 75% reduction of out-of-spec lots on the receiving doc.”
Bill Besson, Quality Assurance Director, Chelsea Milling (aka Jiffy Mix)
%
Most of our customers find 80% (or more) of their suppliers already connected to TraceGains.
Nonconformances aren’t worth the risk
With a majority of food and beverage leaders searching for new suppliers and continuing to report supply chain-related losses, it’s crucial to ensure that the materials you receive match both your expectations and your specs.
We don’t have to explain to you what can happen when the wrong ingredient or out-of-spec batch gets into production. Take control of supplier compliance with complete visibility from received lot information to quality assurance and beyond.
Keep Exploring
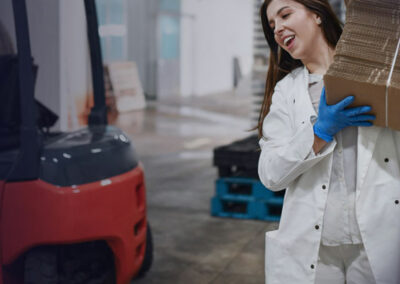
A Day in the Life of Material Compliance
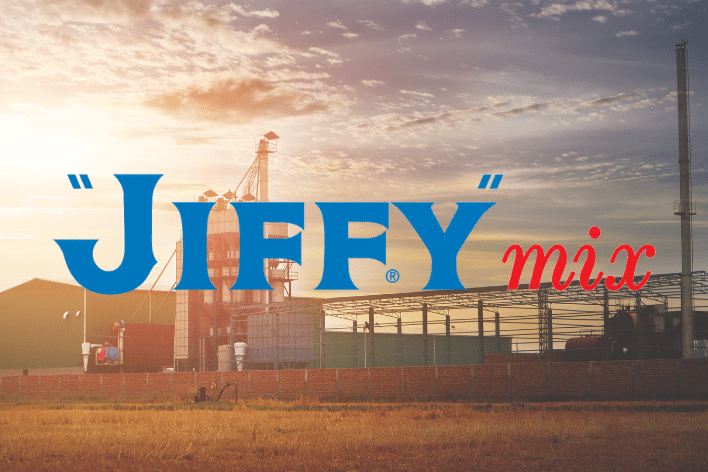
Jiffy Mix
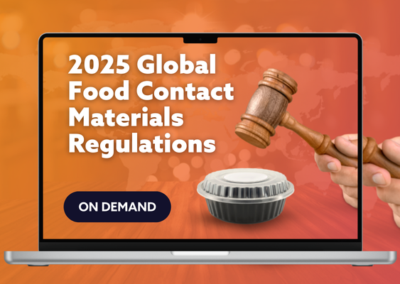